Introduction
In the fast-evolving world of electronics, the demand for advanced materials is continuous. These materials can meet the challenges of miniaturization, durability, and efficient energy management.
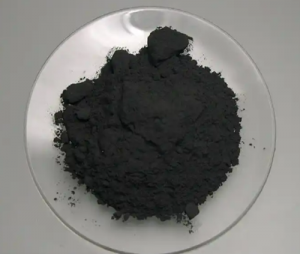
Tungsten alloys are notable for their exceptional properties. They have emerged as key players in the realm of electronic components. This article is going to discuss the features and uses of these alloys. Hope that you can learn about the development of these devices.
Properties of Tungsten Alloys
Tungsten alloys are typically composed of tungsten. They have other elements such as nickel, copper, or iron. Also, they possess a set of properties that make them uniquely suited for electronic applications.
Related reading: 3 Primary Uses Of Tungsten | The Applications Of Tungsten
1. High Density and Compact Size
Tungsten alloys boast an impressive density. This feature allows for the creation of compact yet heavy components. It is crucial in the manufacturing of small electronic devices, where space efficiency is paramount.
The high density of W alloys enables the miniaturization of components without compromising their performance. So, they become ideal for applications in smartphones, laptops, and other portable gadgets.
2. Excellent Electrical Conductivity
One of the primary reasons those alloys are sought after in electronics is their outstanding electrical conductivity. This property ensures efficient and reliable conduction of electrical currents.
That’s a critical requirement for components like connectors, switches, and various electronic contacts. The use of W alloys in these applications contributes to the overall performance and longevity of electronic devices.
3. Resistance to Wear and Corrosion
They exhibit remarkable resistance to wear and corrosion. In the dynamic environment of electronic devices, components are frequently in contact with each other or exposed to varying environmental conditions. And, such resistance is invaluable.
W alloy-coated components include connectors and switches. They can maintain their functions over extended periods. These components also enhance the durability of electronic devices.
4. High Melting Point and Thermal Conductivity
The high melting point of W alloys comes with their excellent thermal conductivity. Thus, they are suitable for applications where heat management is crucial.
Electronic devices often generate heat during operation, and these alloys help dissipate this heat efficiently, preventing overheating and ensuring the device’s optimal performance.
Applications in Electronics

1. Microelectronics and Semiconductors
Tungsten alloys play a vital role in the manufacturing of microelectronics and semiconductors.
Their use as conductive materials is in integrated circuits and semiconductor devices. These parts help improve the overall efficiency and reliability of these components.
Their compatibility with semiconductor manufacturing processes further cements their importance in the electronics industry.
2. Connectors and Contacts
Connectors and contacts are critical components in electronic devices, and they promote the flow of electrical signals.
W alloys possess high electrical conductivity and resistance to wear. They are commonly employed in the production of these components.
Whether in intricate connectors for printed circuit boards or precision contacts within switches, these alloys contribute to the seamless functionality of electronic devices.
3. Electrical Contacts in Switchgear
Switchgear controls the flow of electricity in electrical power systems. It relies on materials that can withstand high electrical currents and provide reliable performance.
W alloys stand out for their robust electrical conductivity and durability. These alloys are frequently used in the production of electrical contacts for switchgear applications. They can ensure safe and efficient power distribution.
Related reading: Tungsten Contacts For Electrical Appliances
4. Electronic Packaging
W finds applications in electronic packaging, particularly in components like heat sinks and substrates.
The high thermal conductivity of tungsten alloys aids in efficiently dissipating heat generated by electronic components. So, they prevent thermal damage and maintain the device’s operational integrity.
Looking Ahead: Innovations and Advancements
As the electronics industry continues to push the boundaries of innovation, tungsten alloys are likely to play an increasingly pivotal role.
Ongoing research focuses on further enhancing the properties of tungsten alloys, exploring novel compositions and manufacturing techniques to meet the evolving demands.
Stanford Advanced Materials: A Leader in Tungsten Alloys for Electronics
In this landscape of electronic advancements, Stanford Advanced Materials (SAM) stands out as a leading supplier of high-quality tungsten alloys. SAM provides a diverse range of tungsten alloy products tailored to meet the specific needs of the electronics industry.
Conclusion
In a word, the unique properties of tungsten alloys include high density, excellent electrical conductivity, and resistance to wear. Thus, they are indispensable in the field of electronics. From microelectronics to switchgear, tungsten alloys contribute to the efficiency, durability, and miniaturization of electronic devices.
As technology continues to advance, the role of tungsten alloys in electronics is poised to expand, driving innovation and shaping the future of electronic components. For more information, please check our homepage.
Recent Comments