Introduction
Tantalum Hafnium Carbide (Ta4HfC5) stands at the forefront of innovation. This compound serves as a pivotal material in the construction of critical components for spacefaring endeavors. Its role ranges from rocket propulsion systems to spacecraft shielding. Let’s have a detailed discussion about the features and uses of tantalum hafnium carbide in this article.
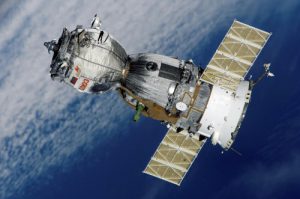
Learning about Ta4HfC5
Tantalum Hafnium Carbide (Ta4HfC5) is renowned for its exceptional properties. This compound is composed of tantalum, hafnium, and carbon. It boasts an impressive melting point exceeding 3,900 degrees Celsius. Thus, it has extraordinary resistance to extreme temperatures and harsh environments.
Ta4HfC5 has become a standout material in various industrial applications. It is a key element in aerospace technology particularly. This compound serves in critical roles such as rocket nozzles, spacecraft components, and heat shields. These uses show its diverse uses and significance in extreme conditions.
Related reading: Top 10 Materials With The Highest Melting Point In The World
The Resilience of Ta4HfC5 in Space Exploration
–Rocket Nozzles and Propulsion Systems
At the heart of space travel is the propulsion systems. These systems propel rockets beyond Earth’s confines. Ta4HfC5 has exceptional resistance to extreme temperatures. So, it has become an optimal choice for the construction of rocket nozzles.
Ta4HfC5 can endure the blistering heat generated during combustion. This compound preserves structural integrity and ensures the efficient expulsion of gases to achieve propulsion. It can withstand temperatures soaring beyond 3,900 degrees Celsius. It is an essential material for safeguarding the integrity of rocket propulsion systems.
–Crucial Role in Heat Shields
Spacecraft encounters extreme variations in temperature as they traverse different celestial environments. For instance, there is much heat generated during re-entry into Earth’s atmosphere. Ta4HfC5 possesses exceptional heat resistance and stability. It is an invaluable asset in the creation of heat shields.
These shields are made of Ta4HfC5-based materials. They act as a protective barrier. These shields mitigate the intense heat generated during re-entry. In this way, the spacecraft and its occupants remain unharmed.
–Components for Spacecraft
The components of spacecraft must endure the rigors of space. These devices must protect themselves from extreme temperature fluctuations. Ta4HfC5 has robustness and a high melting point. So, it is used in the fabrication of various spacecraft components.
You can find it from structural elements to critical parts within the spacecraft’s instrumentation. The resilience of Ta4HfC5 ensures the longevity of these essential components.
Ta4HfC5: Pioneering Space Exploration
As humanity ventures further into the cosmos, Ta4HfC5, and other advanced materials become increasingly pivotal. It stands out because it can withstand extreme temperatures, preserve structural integrity, and provide unparalleled protection against the harsh conditions of space. These features elevate its status as a cornerstone material in the pursuit of space exploration.
The utilization of Ta4HfC5 in space technology not only ensures the success of missions but also reinforces the safety of spacecraft and astronauts in the universe.
Conclusion
In essence, with its exceptional properties, Tantalum Hafnium Carbide has lots of aerospace applications. It has a critical role in fortifying spacefaring equipment and in our quest to explore the cosmos.
With its help, we can unlock the mysteries of the universe. As space exploration continues to advance, Ta4HfC5 remains an indispensable asset. It guides our aspirations toward the frontiers of the unknown.
Advanced Refractory Metals (ARM) is a leading force in the manufacturing and distribution of Tantalum Hafnium Carbide. ARM is dedicated to delivering top-notch, customized metal products to our valued clientele. Please explore our homepage for more information, if you’re seeking excellence in refractory metal solutions.
Recent Comments