Let’s begin with some basic information.
As a tough and corrosion-resistant alloy, stainless steel has been used since the 20th century. It is composed of about 10.5% chrome and a variety of other elements, which include aluminum, carbon, nickel, molybdenum, nitrogen, sulfur, silicon, titanium, copper, and niobium. The chromium content contributes to its rust-resistance and heat-resistance features. Thanks to all these desirable properties, stainless steel fasteners and other stainless steel parts are widely employed in the construction, automotive, and medical industries.
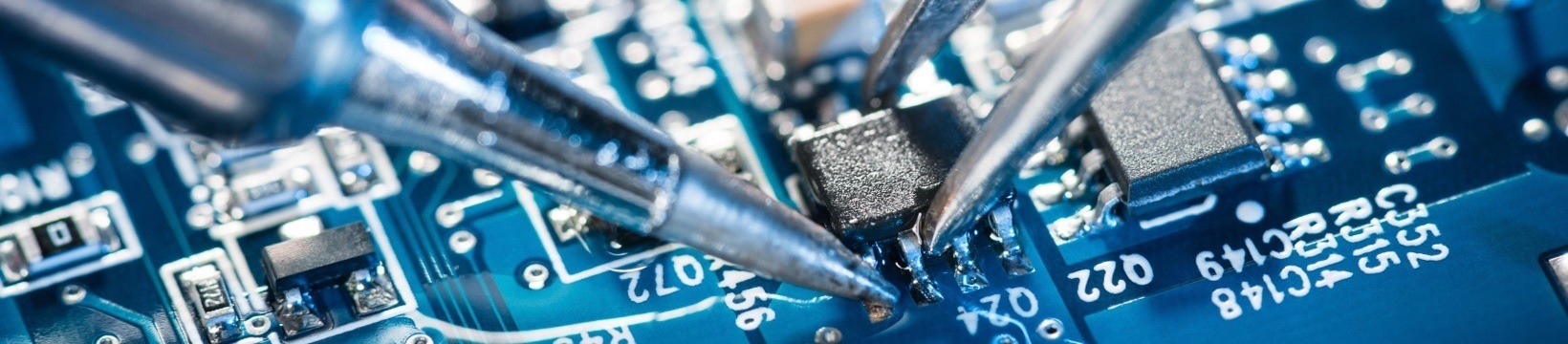
Titanium is a light yet tough metal. Titanium fasteners have a low density of 4.5 g/cm3 and a high strength-to-weight ratio. The melting point of titanium is over 1650 °C and the boiling point is 3287 °C. So, the lustrous silvery metal is perfect for chemical appliances, aircraft skeletons, marine apparatus, and medical equipment.
Stainless Steel VS. Titanium: Corrosion Resistance
Both stainless steel fasteners and titanium fasteners are tough materials that could operate in harsh environments. However, these corrosion-resistant parts have different mechanisms.
Stainless steel fights against rusting with a thin and strong chromium oxide layer, which would regenerate quickly if it is damaged. The susceptibility of certain stainless steel varieties to corrosion depends on their chromium content. A higher proportion of chromium in the metal decreases the likelihood of rust formation. It should be mentioned that stainless steel is not resistant to all corrosive surroundings. Some chemical environments, for example, an aqueous environment containing chloride, may destroy this protective layer, and corrosion follows.
Similarly, titanium oxidizes and forms a thin layer on the surface to prevent the metal from further oxidation. Different from stainless steel, the layer adheres firmly to the metal surface, and will not degrade or peel off over time due to atmospheric exposure. It provides protection against a range of substances, such as organic acids, chloride solutions, and diluted forms of sulfuric and hydrochloric acids. Besides, titanium is a specialty metal with high corrosion resistance and physical stability. So, titanium fasteners possess higher corrosion resistance than stainless steel fasteners, and they are applied to extreme environments involving alkalis, acids, and other industrial chemicals.
In short, Titanium offers excellent corrosion resistance and mechanical stability, while stainless steel exhibits decent mechanical properties but lacks in corrosion resistance.
Stainless Steel VS. Titanium: Strength-to-Density Ratio
Strength-to-density ratio is another striking difference between stainless steel fasteners and titanium fasteners.
Titanium stands out for its strength-to-weight ratio. It has a density of 4.51g/cm³, which is much lower than steel of 7.8-8 g/cm3. In other words, titanium can provide the same amount of strength as steel at 40% of its weight. Such an excellent strength-to-density ratio makes titanium a desirable material to make planes, naval ships, space crafts, and missiles. You can also add aluminum, zirconium, and other elements to improve the properties of titanium parts.
Related reading: How Is Titanium Used In Aerospace/Aeronautics Applications?
Stainless Steel VS. Titanium: Biocompatibility
Both stainless steel bolts and titanium bolts are commonly used in the medical industry.
Because of good biocompatibility with human tissues and blood, titanium fasteners are typically employed to make heart stents, teeth implants, hip balls, and sockets in the human body. These apparatuses are also applied to make surgical instruments such as crutches and wheelchairs.
Stainless steel fasteners are not biocompatible and come with fewer uses. These devices are utilized to make operating tables and steam sterilizers in hygienic environments.
Related reading: Applications Of Titanium Materials In the Medical Industry
Stainless Steel VS. Titanium: How to Choose?
In a word, titanium fasteners are preferred by high-end industries like aerospace and the medical field because of better corrosion resistance, higher strength-to-density ratio, and good biocompatibility, while stainless steel fasteners are suitable for large-scale constructions that have fewer requirements on these properties.
Titanium products are popular in the aerospace industry which puts much more stress on weight than strength. They are also used in the dental and medical industries since titanium is biocompatible and nontoxic. Stainless steel has advantages over titanium when a large quantity is needed for construction. You’ll find stainless steel useful for its weldability and lower cost. At last, here is a table that provides a summary of the differences between stainless steel and titanium.
Recent Comments