Introduction
In the realm of materials science and high-tech industries, the art of crystal growth is a meticulous process that demands precision and reliability. While tantalum crucibles with their unique properties stand at the forefront of this delicate dance. They have become an indispensable tool for flawless crystal growth in various applications.
This article will delve into the critical role of Ta crucibles for precise crystal growth. Hope that you can explore their exceptional attributes and the impact they have on a wide range of industries.
Understanding Tantalum Crucibles
Tantalum crucibles are born from the high-purity tantalum. Such crucibles set the stage for precision in crystal growth. The material’s innate resistance to corrosion and exceptional durability become the foundation of the intricate process.
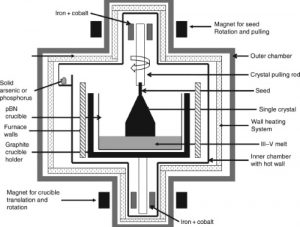
Advantages of Tantalum Crucibles for Crystal Growth
With exceptional properties, tantalum crucibles collectively redefine the standards of crystal growth in the following ways:
1. High-Temperature Stability:
First, Ta crucibles stand out for their thermal performance. So, the controlled environment within tantalum crucibles is conducive to high-temperature processes like crystal growth. Also, tantalum’s high melting point ensures stability, so Ta crucibles can withstand the intense heat necessary to initiate and sustain crystal formation.
2. Minimizing Contaminants:
Second, the seamless nature of tantalum crucibles minimizes the risk of contamination during crystal growth. Their impermeable structure serves as a protective shield. Therefore, the resulting crystals remain pure and untainted by external elements.
3. Versatility in Crystal Types:
Tantalum crucibles exhibit versatility in accommodating various crystal types. Whether cultivating crystals for semiconductor devices, optoelectronics, or other cutting-edge applications, these crucibles provide a controlled environment conducive to precise crystal growth.
4. Consistency in Results:
The uniformity of tantalum crucibles contributes to consistency in crystal growth results. This predictability is essential in research and manufacturing since the reproducibility of crystal structures is paramount for achieving desired material properties.
5. Reducing Thermal Stress:
Tantalum is also noted for its thermal conductivity and resistance to thermal shock. These features play a pivotal role in minimizing thermal stress during crystal growth. This ensures a gradual and controlled cooling process and prevents structural deformities in the emerging crystals.
Applications of Crystal Growth Using Tantalum Crucibles
The applications of such crystal growth span a diverse array of industries. All those applications benefit from the precision, durability, and purity.
1. Applications in Semiconductor Manufacturing:
Tantalum crucibles find a special place in semiconductor manufacturing because the precision of crystal growth directly impacts the performance of electronic components. The controlled environment provided by these crucibles contributes to the production of high-quality semiconductor materials.
2. Advancements in Nanotechnology:
As nanotechnology continues to advance, Ta crucibles play a vital role in the creation of nanoscale crystals. They facilitate controlled growth at the atomic and molecular levels and meet the demands of this burgeoning field.
3. Future Innovations:
Looking forward, these crucibles are poised to be integral to future innovations in crystal growth technology. Researchers and engineers continually explore ways to enhance the precision and efficiency of crystal growth processes. And tantalum crucibles serve as a key enabler of these advancements.
Related reading: Tantalum Crucible in Materials Research and Synthesis
Conclusion
In the intricate world of crystal growth, tantalum crucibles emerge as important tools. They are indispensable because they offer a controlled, contamination-resistant environment for the delicate dance of crystal formation. As industries continue to push the boundaries of materials science, these crucibles stand as a testament to the synergy of craftsmanship and technology, shaping the crystals that power the future.
At Stanford Advanced Materials (SAM), a diverse range of tantalum crucibles in various dimensions are available for purchase. SAM stands as a trusted supplier of various tantalum products. Custom tailoring options upon request are also available. Please do not hesitate to contact us.
Reference:
[1] Pallab Bhattacharya, Roberto Fornari and Hiroshi Kamimura (2011). Comprehensive Semiconductor Science and Technology. https://www.sciencedirect.com/referencework/9780444531537/comprehensive-semiconductor-science-and-technology#book-info
Recent Comments